1.¿Qué es el acero?
-El término acero sirve comúnmente para denominar, en ingeniería metalúrgica, a una aleación de hierro con una cantidad de carbono variable entre el 0,03% y el 1,075% en peso de su composición, dependiendo del grado. Si la aleación posee una concentración de carbono mayor al 2,0% se producen fundiciones que, en oposición al acero, son mucho más frágiles y no es posible forjarlas sino que deben ser moldeadas.
- El acero conserva las características metálicas del hierro en estado puro, pero la adición de carbono y de otros elementos tanto metálicos como no metálicos mejora sus propiedades fisico-químicas. A pesar de su densidad (7850 kg/m³ de densidad en comparación a los 2700 kg/m³ del aluminio, por ejemplo) el acero es utilizado en todos los sectores de la industria, incluso en el aeronáutico, ya que las piezas con mayores solicitaciones (ya sea a impacto o fatiga) sólo pueden aguantar con un material como el acero.

1.1 Microconstituyentes, estructuras cristalinas.
Microconstituyentes:
El hierro puro presenta tres estados alotrópicos a medida que se incrementa la temperatura desde la temperatura ambiente.
- Hasta los 911 °C, el hierro ordinario, cristaliza en el sistema cúbico centrado en el cuerpo (BCC) y recibe la denominación de hierro α o ferrita. Es un material dúctil y maleable responsable de la buena forjabilidad de las aleaciones con bajo contenido en carbono y esferromagnético hasta los 768 °C (temperatura de Curie a la que pierde dicha cualidad). La ferrita puede disolver muy pequeñas cantidades de carbono.
- Entre 911 y 1400 °C cristaliza en el sistema cúbico centrado en las caras (FCC) y recibe la denominación de hierro γ oaustenita. Dada su mayor compacidad la austenita se deforma con mayor facilidad y es paramagnética.

- Entre 1400 y 1538 °C cristaliza de nuevo en el sistema cúbico centrado en el cuerpo y recibe la denominación de hierro δ que es en esencia el mismo hierro alfa pero con parámetro de red mayor por efecto de la temperatura, a mayor temperatura el hierro se encuentra en estado líquido.

- Si se añade carbono al hierro, sus átomos podrían situarse simplemente en los intersticios de la red cristalina de éste último; sin embargo en los aceros aparece combinado formando carburo de hierro (Fe3C), es decir, un compuesto químico definido y que recibe la denominación decementita de modo que los aceros al carbono están constituidos realmente por ferrita y cementita.
2.Caracteristicas físicas de los aceros:
-Es difícil establecer las propiedades físicas y mecánicas del acero debidoa que estas varían con los ajustes en su composición, en los
diversos tratamientostérmicos, químicos o mecánicos, con los que pueden conseguirse aceros concombinaciones de características adecuadas para infinidad de aplicaciones, se pueden citar algunas propiedades genéricas:

-Su densidad media es de 7850 kg/m³. En función de la temperatura el acero sepuede contraer, dilatar o fundir.

- El punto de fusión del acero depende del tipo de aleación y los porcentajes de elementos aleantes. El de su componente principal, el hierro es de alrededorde 1.510 °C en estado puro (sin alear), sin embargo el acero presentafrecuentemente temperaturas de fusión de alrededor de 1.375 °C, y en generalla temperatura necesaria para la fusión aumenta a medida que se aumenta elporcentaje de carbono y de otros aleantes, (excepto las aleaciones auténticasque funden de golpe). Por otra parte el acero rápido funde a 1.650 °C. Su puntode ebullición es de alrededor de 3.000 °C.

- Tenacidad:
Es la capacidad que tiene un material de absorber energía sin producir fisuras(resistencia al impacto). El acero es un material muy tenaz, especialmente en alguna de las aleaciones usadas para fabricar herramientas.

- Ductilidad:
Es relativamente dúctil. Con él se obtienen hilos delgados llamados alambres.Un aumento de la temperatura en un elemento de acero provoca un aumentoen la longitud del mismo.
(coeficiente de dilatación pael acaro α = 0,000012)

-Maleabilidad:
Se pueden obtener láminas delgadas llamadas hojalata. La hojalata es
unalamina de acero, de entre 0,5 y 0,12 mm de espesor, recubierta, generalmentede forma electrolítica, por estaño.

- Dureza:
La densidad promedio del acero es 7850 kg/m3. Es la resistencia que ofrece un acero para dejarse penetrar. La dureza de los aceros varía entre la del hierro yla que se puede lograr mediante su aleación u otros procedimientos térmicos o químicos, conservar un núcleo tenaz en la pieza que evite fracturas frágiles.

Aceros típicos con un alto grado de dureza superficial son los que se empleanen las herramientas de mecanizado, denominados aceros rápidos quecontienen cantidades significativas de cromo, wolframio, molibdeno y vanadio. Los ensayos tecnológicos para medir la dureza son Brinell, Vickers y Rockwell, entre otros.
3.Diagrama Hierro-Carbono:
-En el diagrama de equilibrio o de fases, Fe-C se representan las transformaciones que sufren los aceros al carbono con la temperatura, admitiendo que el calentamiento (o enfriamiento) de la mezcla se realiza muy lentamente de modo que los procesos de difusión de temperatura (homogeneización) tienen tiempo para completarse. Dicho diagrama se obtiene experimentalmente identificando los puntos críticos —temperaturas a las que se producen las sucesivas transformaciones— por métodos diversos.
-Microconstituyentes: vease el punto 1.1 donde esta detallado.
- Transformación de la austenita:
- Un Eutéctico (composición para la cual el punto de fusión es mínimo) que se denomina ladeburita y que contiene un 4,3% de carbono (64,5 % de cementita). La ledeburita aparece entre los constituyentes de la aleación cuando el contenido en carbono supera el 2% (región del diagrama no mostrada) y es la responsable de la mala forjabilidad de la aleación marcando la frontera entre los aceros con menos del 2% de C (forjables) y las fundiciones con porcentajes de carbono superiores (no forjables y fabricadas por moldeo). De este modo se observa que por encima de la temperatura crítica los aceros están constituidos sólo por austenita, una solución sólida de carbono en hierro γ y su microestructura en condiciones de enfriamiento lento dependerá por tanto de las transformaciones que sufra ésta.
- Un Eutectoide en la zona de los aceros, equivalente al eutéctico pero en estado sólido, donde la temperatura de transformación de la austenita es mínima. El eutectoide contiene un 0,77 %C (13,5% de cementita) y se denomina perlita. Está constituido por capas alternas de ferrita y cementita, siendo sus propiedades mecánicas intermedias entre las de la ferrita y la cementita.

-Otros microconstituyentes: Las texturas básicas descritas (perlíticas) son las obtenidas enfriando lentamente aceros al carbono, sin embargo modificando las condiciones de enfriamiento (base de los tratamientos térmicos) es posible obtener estructuras cristalinas diferentes.
- La martentisa es el constituyente típico de los aceros templados y se obtiene de forma casi instantánea al enfriar rápidamente la austenita. Es una solución sobresaturada de carbono en hierro alfa con tendencia, cuanto mayor es el carbono, a la sustitución de la estructura cúbica centrada en el cuerpo por tetragonal centrada en el cuerpo. Tras la cementita (y los carburos de otros metales) es el constituyente más duro de los aceros.

- Velocidades intermedias de enfriamiento dan lugar a la bainita, estructura similar a la perlita formada por agujas de ferrita y cementita pero de mayor ductilidad y resistencia que aquélla.
- También se puede obtener austenita por enfriamiento rápido de aleaciones con elementos gammágenos (que favorecen la estabilidad del hierro γ) como el níquel y el manganeso, tal es el caso por ejemplo de los aceros inoxidables austeníticos.

Austenita (hierro-γ duro)
Ferrita (hierro-α. blando)
Cementita (carburo de hierro. Fe3C)
Perlita (88% ferrita, 12% cementita)
Ledeburita (ferrita - cementita eutectica, 4.3% carbón)
Bainita
Martensita
4. Clasificación de los aceros en función del porcentaje de carbono.
Clasificación del acero por su contenido de Carbono:
- Aceros Extrasuaves: el contenido de carbono varia entre el 0.1 y el 0.2 %
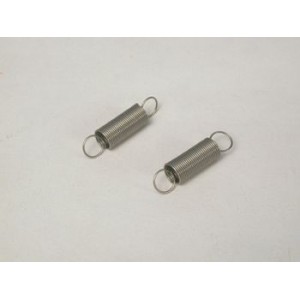
- Aceros suaves: El contenido de carbono esta entre el 0.2 y 0.3 %
- Aceros semisuaves: El contenido de carbono oscila entre 0.3 y el 0.4 %

- Aceros semiduros: El carbono esta presente entre 0.4 y 0.5 %

- Aceros duros: la presencia de carbono varia entre 0.5 y 0.6 %

- Aceros extraduros: El contenido de carbono que presentan esta entre el 0.6 y el 07 %
5. Relación entre características físicas y tamaño de grano.
-El crecimiento del grano ocurre debido al proceso de coagulación y reorientación del los granos adjuntos y esto es función de el tiempo y la temperatura.
Conforme la temperatura aumenta, la rigidez de la red disminuye produciendo un incremento en la rapidez de crecimiento del grano.
Los granos grandes tienen menor energía libre que los de tamaño menor. Esto esta asociado con la menor cantidad de área de frontera de grano y esta relacionada con la fuerza que impulsa el crecimiento del grano.
Dicho lo anterior; el tamaño final del grano estará determinado por los parámetros de la energía libre del grano y el grado de rigidez de la red cristalina.
Por tanto, la nucleación y el posterior crecimiento del grano comprendidos en el proceso de recocido serán los factores a controlar para la obtención de propiedades ultimas acorde con las necesidades. Si se favorece una nucleación rápida y un crecimiento lento se obtendrá como resultado un material de grano fino con el incremento en la tenacidad o resistencia al impacto con el aumento en la dureza; en cambio, si la nucleación es lenta y el crecimiento del grano es rápido en tamaño del grano será grueso con el resultado de que el metal disminuye su tenacidad y su maquinabilidad y en cambio aumenta su ductilidad.

6. Aleantes y características que aportan al acero.
- En las aleaciones se pretende conseguir unas características determinadas como templabilidad, resistencia mecanica, dureza, tenacidad, resistencia al desgaste, soldabilidad o maquinabilidad.
Lista de elementos que se pueden alear con el Sr. Acero:
-Aluminio: se usa en algunos aceros de nitruración al Cr-Al-Mo de alta dureza en concentraciones cercanas al 1% y en porcentajes inferiores al 0,008% como desoxidante en aceros de alta aleación.
-Boro: En muy pequeñas cantidades (del 0,001 al 0,006%) aumenta la templabilidad sin reducir la maquinabilidad, pues se combina con el carbono para formar carburos proporcionando un revestimiento duro. Es usado en aceros de baja aleación en aplicaciones como cuchillas de arado y alambres de alta ductilidad y dureza superficial.
- Cobalto: muy endurecedor. Disminuye la templabilidad. Mejora la resistencia y la dureza en caliente. Es un elemento poco habitual en los aceros. Aumenta las propiedades magnéticas de los aceros. Se usa en los aceros rápidos para herramientas y en aceros refractarios.
- Cromo: Forma carburos muy duros y comunica al acero mayor dureza, resistencia y tenacidad a cualquier temperatura. Solo o aleado con otros elementos, mejora la resistencia a la corrosión, se usa en aceros inoxidables, aceros para herramientas y refractarios. También se utiliza en revestimientos embellecedores o recubrimientos duros de gran resistencia al desgaste, como émbolos, ejes, etc.
- Molibdeno: Aumenta mucho la profundidad de endurecimiento de acero, así como su tenacidad, mejorar la resistencia a la corrosión.
- Nitrógeno: Se agrega a algunos aceros para promover la formación de austenita.
- Níquel: Es un elemento gammageno permitiendo una estructura austenítica a temperatura ambiente, que aumenta la tenacidad y resistencia al impacto.
- Plomo: El plomo no se combina con el acero, se encuentra en él en forma de pequeñísimos glóbulos, como si estuviese emulsionado, lo que favorece la fácil mecanización por arranque de viruta, (torneado, cepillado, taladrado, etc.) ya que el plomo es un buen lubricante de corte, el porcentaje oscila entre 0,15% y 0,30% Se añade a algunos aceros para mejorar mucho la maquinabilidad.
- Silicio: aumenta moderadamente la templabilidad. Se usa como elemento desoxidante. Aumenta la resistencia de los aceros bajos en carbono.
- Titanio: se usa para estabilizar y desoxidar el acero, mantiene estables las propiedades del acero a alta temperatura. Se utiliza su gran afinidad con el Carbono para evitar la formación de carburo de hierro al soldar acero.
- Wolframio: también conocido como tungsteno. Forma con el hierro carburos muy complejos estables y durísimos, soportando bien altas temperaturas. En porcentajes del 14 al 18 %, proporciona aceros rápidos con los que es posible triplicar la velocidad de corte de los aceros al carbono para herramientas.
- Vanadio: posee una enérgica acción desoxidante y forma carburos complejos con el hierro, que proporcionan al acero una buena resistencia a la fatiga, tracción y poder cortante en los aceros para herramientas.
24 febrero 2012. El sector industrial se verá beneficiado con esta nueva aleación de acero bainítico con boro.

7. Tratamientos térmicos.
- Fundición Nodular.
Es una
aleación Fe-C y Si, cuya microestructura está conformada por una matriz
metálica y una cantidad del 10 al 15% de grafito en forma de esferas. La
presencia de grafito afecta ciertas propiedades entre ellas la
disminución de la dureza y la resistencia mecánica, pero por otro lado,
incrementa la maquinabilidad.
-Ferríticas: Posee maquinabilidad, ductilidad y límite elástico moderado.
-Perlíticas: Buen límite elástico y ductilidad pero baja maquinabilidad, se pueden templar superficialmente.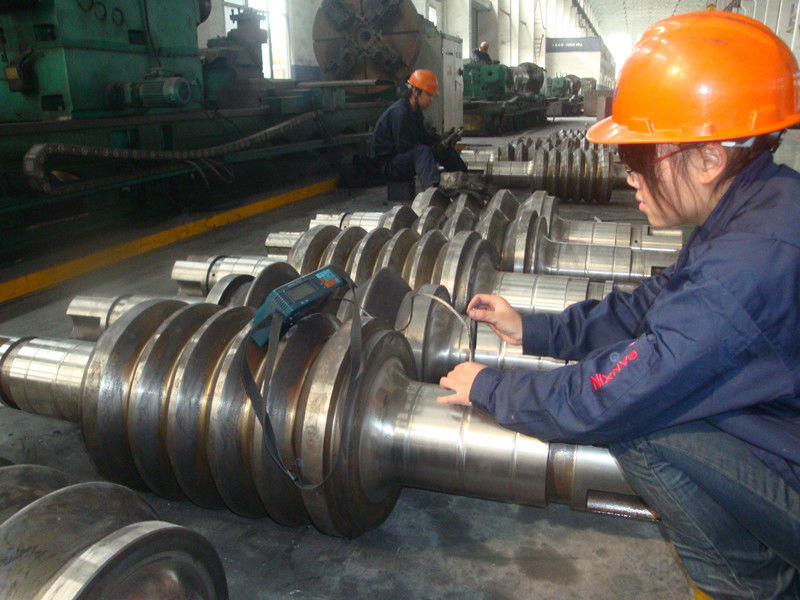
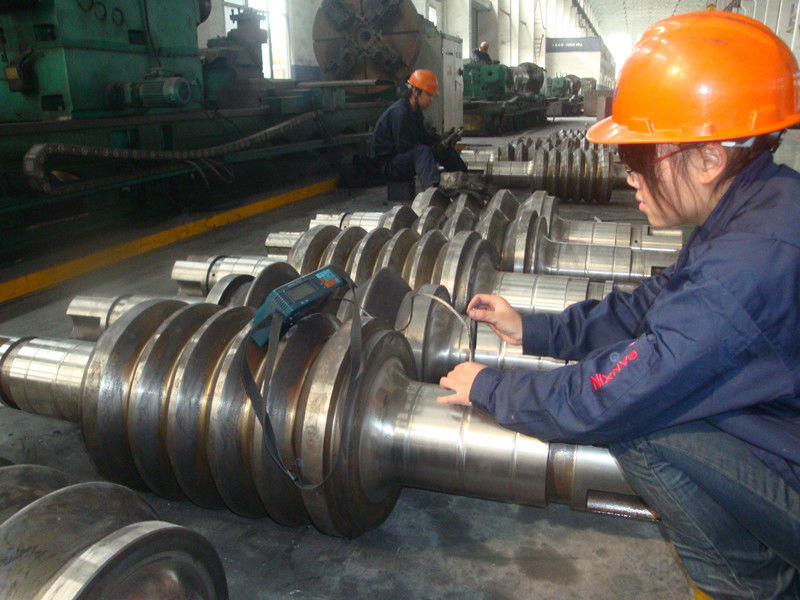
-Tratadas térmicamente: Con
tratamientos térmicos como normalizados, templados y revenidos o
austemperadas, presentan alta resistencia a la tracción y alto límite
elástico.

La fundición nodular presenta una mayor
resistencia a la tracción que la fundición gris y se suele utilizar para
la fabricación de válvulas y engranajes de alta resistencia, cuerpos de
bomba, cigüeñales y pistones. Se diferencia de la maleable porque
generalmente se obtiene como resultado de la solidificación y no
requiere tratamiento térmico.
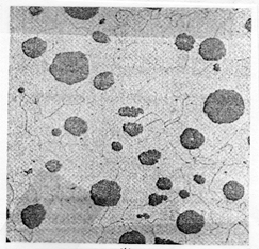
Esferoides de grafito sobre una matriz de ferrita. Microestructura fundición nodular
Temple y revenido: bonificado
Después que se ha endurecido el acero es muy quebradizo o frágil lo que impide su manejo pues se rompe con el mínimo golpe debido a la tensión interior generada por el proceso de endurecimiento. Para contrarrestar la fragilidad se recomienda el temple del acero (en algunos textos a este proceso se le llama revenido y al endurecido temple). Este proceso hace más tenaz y menos quebradizo el acero aunque pierde algo de dureza. El proceso consiste en limpiar la pieza con un abrasivo para luego calentarla hasta la temperatura adecuada (ver tabla), para después enfriarla al intemperie en el mismo medio que se utilizó para endurecerla.Color | Grados C | Tipos de aceros |
---|---|---|
Paja claro | 220 | Herramientas como brocas, machuelos |
Paja mediano | 240 | Punzones dados y fresas |
Paja oscuro | 255 | Cizallas y martillos |
Morado | 270 | Árboles y cinceles para madera |
Azul obscuro | 300 | Cuchillos y cinceles para acero |
Azul claro | 320 | Destornilladores y resortes |
Recocido
El recocido es el tratamiento térmico que, en general, tiene como finalidad principal el ablandar el acero u otros metales, regenerar la estructura de aceros sobrecalentados o simplemente eliminar las tensiones internas que siguen a un trabajo en frío. (Enfriamiento en el horno). Esto es, eliminar los esfuerzos residuales producidos durante el trabajo en frío sin afectar las propiedades mecánicas de la pieza finalizada, o puede utilizarse el recocido para eliminar por completo el endurecimiento por deformación. En este caso, la parte final es blanda y dúctil pero sigue teniendo un acabado de superficie y precisión dimensional buenos. Después del recocido, se puede realizar un trabajo en frío adicional dado que la ductilidad se restaura; al combinar ciclos de repetición de trabajo en frío y recocido, pueden alcanzarse deformaciones totales grandes..
El término "recocido" también se utiliza para describir otros tratamientos térmicos. Por ejemplo, los vidrios pueden tratarse de manera térmica o recocerse para eliminar los esfuerzos residuales presentes en el mismo. Los hierros y aceros pueden recocerse para maximizar sus propiedades, en este caso la ductilidad, aun cuando no se haya trabajado con el material en frío.
Existen 3 etapas consideradas como las más importantes en el proceso de recocido:
-Recuperación
La microestructura original trabajada a bajas temperaturas está compuesta de granos que se encuentran deformados que contienen un gran número de dislocaciones entrelazadas unas con otras. Cuando se calienta primero el metal, la energía térmica adicional permite que las dislocaciones se muevan y formen los límites de una estructura subgranular poligonizada. Lo anterior significa que conforme el material se va calentando, las dislocaciones van desapareciendo y a su vez los granos toman mayor tamaño. Sin embargo, la densidad de las dislocaciones permanece virtualmente sin cambiar. Este tratamiento a temperatura baja elimina los esfuerzos residuales debidos al trabajo en frío sin ocasionar un cambio en la densidad de las dislocaciones y se le llama recuperación. Por último, la recuperación frecuentemente agiliza la resistencia a la corrosión de los materiales.-Recristalización
Cuando se somete a muy altas temperaturas un metal trabajado en frío previamente, la recuperación rápida elimina los esfuerzos residuales y produce la estructura de las dislocaciones poligonizadas. Durante este instante ocurre la formación de núcleos de pequeños granos en los límites de las celdas de la estructura poligonizada, eliminando la mayoría de las dislocaciones. Debido a que el número de dislocaciones se reduce en grande escala, el metal recristalizado tiene una resistencia baja pero una gran ductilidad. Se denomina como temperatura de recristalización a la temperatura a la cual aparece una microestructura de granos nuevos que tienen pocas dislocaciones. Recristalización es el proceso durante el cual se forman granos nuevos a través del tratamiento térmico a un material trabajado en frío. La temperatura de recristalización depende de varias variables, por lo tanto no es una temperatura fija
-Crecimiento de granos
Cuando las temperaturas aplicadas en el recocido son muy altas, las etapas de recuperación y de recristalización ocurren de una forma más rápida, produciéndose así una estructura de granos más fina. Si la temperatura es lo bastante alta, los granos comienzan a crecer, con granos favorecidos que eliminan a los granos que son más pequeños. Este fenómeno, al cual se le puede denominar como crecimiento de granos, se lleva a cabo por medio de la reducción en el área de los límites de los granos. En la mayoría de los materiales ocurrirá el crecimiento de grano si se mantienen a una temperatura lo suficientemente alta, lo cual no se encuentra relacionado con el trabajo en frío. Esto quiere decir que la recristalización o la recuperación no son indispensables para que los granos puedan crecer dentro de la estructura de los materiales.Los materiales cerámicos que presentan un endurecimiento casi nulo muestran una cantidad considerable de crecimiento de granos. Asimismo, puede ocurrir un crecimiento anormal de granos en algunos materiales como resultado de una formación de fase líquida.
Tipos de recocido:
-Recocido de homogeneización
En el recocido de homogeneización, propio de los aceros hipoeutectoides, la temperatura de calentamiento es la correspondiente a+200 °C sin llegar en ningún caso a la curva de sólidos, realizándose en el propio horno el posterior enfriamiento lento, siendo su objetivo principal eliminar las heterogeneidades producidas durante la solidificación.-Recocido de regeneración
También llamado normalizado, tiene como función regenerar la estructura del material producido por temple o forja. Se aplica generalmente a los aceros con más del 0.6% de C, mientras que a los aceros con menor porcentaje de C sólo se les aplica para finar y ordenar su estructura.ejemplo: Después de un laminado en frío, donde el grano queda alargado y sometido a tensiones, dicho tratamiento devuelve la microestructura a su estado inicial.

-Recocido de globulización
Usado en aceros hipoeutectoides para ablandarlos después de un anterior trabajo en frío. Por lo general se desea obtener globulización en piezas como placas delgadas que deben tener alta embutición y baja dureza. Los valores más altos de embutición por lo general están asociados con la microestructura globulizada que solo se obtiene en un rango entre los 650 y 700 grados centígrados. Temperaturas por encima de la crítica producen formación de austenita que durante el enfriamiento genera perlita, ocasionando un aumento en la dureza no deseado. Por lo general piezas como las placas para botas de protección deben estar globulizadas para así obtener los dobleces necesarios para su uso y evitar rompimiento o agrietamiento. Finalmente son templadas para garantizar la dureza. Es usado para los aceros hipereutectoides, es decir con un porcentaje mayor al 0,89 % de C, para conseguir la menor dureza posible que en cualquier otro tratamiento, mejorando la maquinabilidad de la pieza. ejemplo: El ablandamiento de aceros aleados para herramientas de más de 0.8% de C.
No hay comentarios:
Publicar un comentario